I am a big fan of Mike Burrows, and have mentioned his work quite a few times over the years at Bicycle Design. In 2012, lifelong “cycling fanatic” and engineer Karl Sparenberg of Advanced Velo Design took over production of Burrows’ Windcheetah recumbent trike, and has been working on improving the materials and manufacturability of the original design. I think it’s a pretty interesting story, so I am letting Karl tell it to you directly in the guest post below.
Having taken over the production of Windcheetah’s a couple of years ago the design and manufacturing has taken a different tack.
Many people are already aware of Windcheetah’s so I’ve decided not to rattle on with all the historic detail… but it goes without saying that Mike Burrows did a pretty good job 30 or so years ago when he designed it!!
But please do note that the modern iteration of Windcheetah is now a more cutting edge speed machine, incorporating advanced materials including Carbon composites and Titanium that were still prohibitively expensive in years gone by, and with that we have to move with the times and produce a ‘better’ machine.
When I took over the manufacture Windcheetah, to my alarm there was an Achilles heel, not with the design but the castings. These are the components that make up the frame, by bonding the aluminum and carbon tubes together onto spigots, these sand cast aluminum components could come from the foundry with flaws or voids in them.
If you could imagine ordering a ‘set’ of castings to make a Windcheetah frame and then having to go through the whole long winded process of post casting heat treatment, machining, drilling, tapping, powder coating and then the final finishing, only then can you proceed onto the bonded assembly with the tubing.
At any stage in this manufacturing process, from the rough sand castings to the finished component can the dreaded ‘flaws’ or ‘voids’ be discovered. Even worse, if the frame has been fully assembled and the sand casted part fails during testing, not only would the whole frame have to be scrapped, but it would also take out any of the other perfectly good components and tubing to the scrap bin with it. A very expensive and time consuming process as I’m sure you could imagine… there had to be a better way to manufacture these components!?
You may be interested to know, why were the sand castings failing at such an unacceptably high rate? Well, a few things really, but predominantly the foundries in the UK had to compete with the far east for business and as a consequence many of them had to shut down, leaving in short, foundries that were not tooled up for small production runs, or the necessary skills to cast such intricate shapes, as you find on a WIndcheetah. The foundry would simply credit the customer if any of the components failed. But this gesture didn’t really help, when what was required was a full set of components to build a machine, not the hassle and cost implication of trying to manage the ongoing balance of the failure in certain components, while the ‘perfect’ odd parts sat on the shelf.
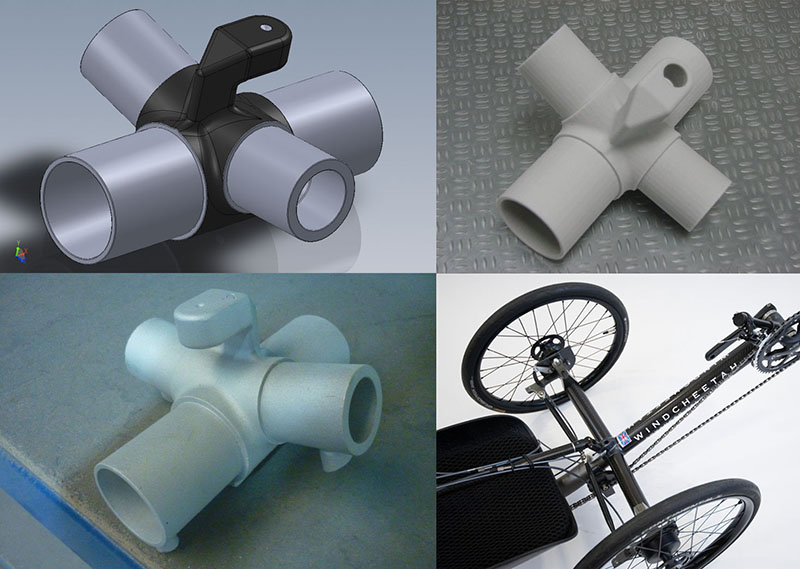
Top: CAD model screenshot and a 3d printed part (used to produce the soft mold needed for wax production).
The solution became apparent after considerable research into an alternative method of manufacturing and with massive investment into the tooling for a process known as ‘lost wax’ or ‘Investment casting’, the two terms are interchangeable but in essence the same thing
So what you see below is the result of numerous hours of redesign and CAD drawing to be able to 3D print the parts ready for soft mould production that manufacture the waxes. Now we can produce waxes this opens up the possibilities of alternative materials to Aluminum. Shortly we will be bringing to market a Magnesium version as soon as Beta testing is completed. The advantages of Magnesium or Aluminium are instantly a weight saving of third the weight.
So watch this space for an even quicker, lighter and more performance orientated Windcheetah.
For further detail contact me directly karl@windcheetah.co.uk
Subscribe to the email newsletter, and follow Bicycle Design on Facebook , Twitter , Pinterest , and Google + … and now on Instagram too!